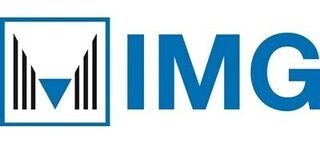
- Ship Transfer System
- Automated plant technology for complex large structures
- Machining centres for profile and pipe production
- Transport systems
- Special machines
- Robotic welding systems
- Shipyard & factory planning
IMG mbH as a system supplier and engineering service provider is one of the leading vendors worldwide of complex plant and transport technology for companies in the shipbuilding, machine construction, structural steelwork and wind energy industries.
Panel Lines
IMG mbH panel production lines are optimally tailored to the needs of our customers. The panel production lines are made up of stationary and mobile facilities and have varying degrees of automation and mechanisation. The most common application will be panel production in shipbuilding or production lines for bridge panels in the construction sector.Depending on the industry and area of application, we distinguish between the following variants:
Panel lines are important production lines especially in the shipbuilding sector. The biggest effects are achieved with regard to the following points:
- increase in productivity
- capacity expansion
- quality improvement
- faster throughput times
- improvement in working conditions
Panel lines consists of stationary and mobile facilities and have varying degrees of automation and mechanisation:
- Welding gantries for one or two sided butt seam welding
- Turning devices, for example, to turn flat panels
- Gantries for marking and contour cutting
- Profile mounting and tack welding gantries
- Units for fillet seam welding
- Assembly gantries
- Transport systems, e.g. roller conveyors, friction drives, chain conveyors, lifting and transport trucks
- Discharge facilities
- Gantries for welding robots in combination with active 3D image recognition
Robot Welding Gantry with Tilting Table
The gantry serves as a base for the welding robot and the welding support robot. There are 11 robot axes in total that can be used during welding. The welding support robot is used in "slave mode" to clean the brushes and grinders of the interlayers. The welding system is movable on tracks so as to supply the tilting table with the clamping and handling device. The tilting table is an additional component of the pipe welding system. Designed as the longitudinal axis of the welding portal, the tilting table enables continuous PA position welding together with the rotating axis of the changing frame during the automatedwelding process.
MACHINING CENTRES FOR PROFILE AND PIPE PRODUCTION
SPECIAL MACHINES FOR PRODUCTIVITY AND DIMENSIONAL ACCURACY
When prefabricating individual parts in shipbuilding and structural steelwork the rod-shaped components profiles and pipes are of great importance. Considerable increases in productivity and also improvements in the dimensional accuracy of the parts can be achieved through optimally designed production lines and special machines.
IMG supplies production lines and special machines for profile and pipe prefabrication:
- Automatic profile cutting lines with plasma and/or oxyacetylene cutting technology in all kinds of configurations regarding transport and additional facilities (drying units, edge cleaning units and sorting systems)
- Labelling machines for profiles, either as standalone systems or integrated into a transport line, to apply various kinds of labelling and marking such as part lettering, bending lines and markings for cutting to be done manually
- Automated pipe processing lines, starting with the pipe warehouse through to the cutting to size and flanging of the pipes up to the bending of the pipes, for which special machines (such as pipe bending machines) from leading makers are used
- Pipe flange welding machines for the automatic flanging of pipes that have been cut to length.
- The main focus in the profile and pipe production lines and special machines is on offline programming of the line and machine programs to attain the best possible rate of utilization of the systems. Increasing, such lines are equipped with a central controller that works together with the superordinated production planning and control systems.
SHIPYARD & FACTORY PLANNING
Factory planning comprises both planning work for the modernization of existing production facilities and also the complete planning of brand new "green field" production facilities. Working together with the affiliate IEM GmbH, IMG mbH offers planning services to suit any individual customer wish, from the first planning concept with general layouts through to the detailed planning of the individu-al production areas with the arrangement of all the main production units and cranes as shop lay-outs, up to services in approval planning and project management in the implementation phase of the project.
Our factory planning services primarily comprise the following:
- Definition of the starting situation (among other items, taking / processing inventory data at the customer, site assessment, definition of the production program, determining of the working time and shift schedules)
- Drawing up a general layout- variations for the modernisation or new planning for discussion with the customer and joint definition of the preferred variants
- Detailed planning in accordance with the depth of planning defined with the customer
- Technical specifications for the required production facilities and equipment, cranes, transport equipment, etc., on the basis of capacity observations for the implementation of the defined production program
- Concept for the structural and process-oriented organization with a determination of the num-ber of employees and a proposal for a suitable organization structure
- Concepts for logistics, planning and control with proposals for suitable software solutions
- 3D simulation and animation of the entire factory and of individual production processes
HANDLING SYSTEMS
RELIABLE TRANSPORT EVEN IN THE HEAVY LOAD AREA
The safe and timely transport of the starting material and of the intermediate products and modules to the relevant downstream processing stations has a decisive influence on the effectiveness of the production throughput. We have made it our goal to structure these sometimes very complex work flows to be as uncomplicated as possible. We offer our customers both individual and complete solutions for efficient material handling. Our handling systems that are tailored individually to the needs of the customer are subject to constant further development based on our worldwide experience, technical capability and high level of commitment. Our handling systems:
Stationary transport systems
- Roller conveyors
- Chain conveyors
- Lifting devices for panel and profile handling and the interlinking of the same
Special cranes with vacuum or magnet technology
Manually operated cranes
Automatic cranes
Fast gantry cranes, overhead cranes and swivelling booms
- developed for block construction in shipbuilding and also for primary industry and industrial plant construction
Heavy load transport systems
- for the millimetre-precise positioning of large blocks in shipbuilding and the construction of heavy machinery
Frequently the transport facilities of IMG work together with super ordinated central controllers for the production areas and production planning and control systems that represent a further product group of IMG.
LAVGAN DOCKYARD LTD.
LAVGAN, INDIA
Supply of a ship transport system for ships of up to 8,500 tons, consisting of bogies and trestles with hydraulic drive and 2 self propelled power units.
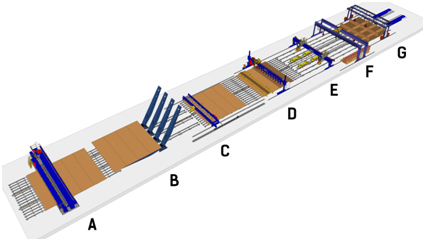
Flat panels
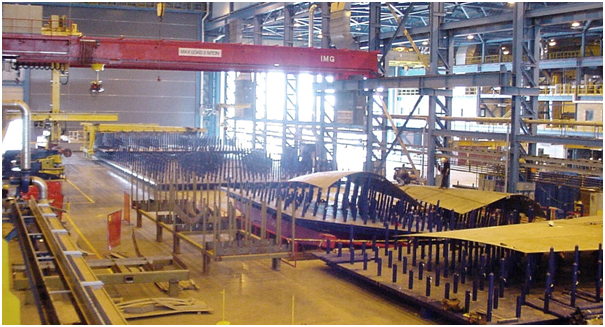
Micro panels
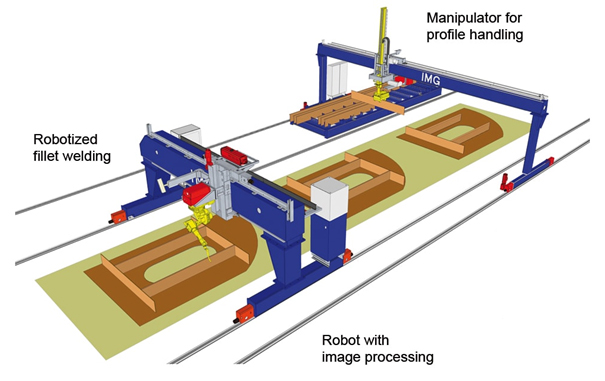
Curved panels
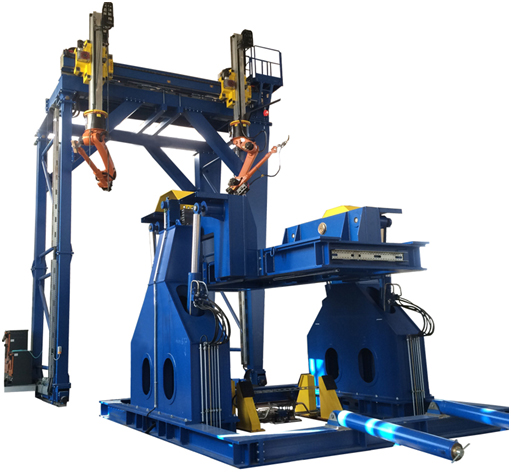
Robot Welding Gantry with Tilting Table
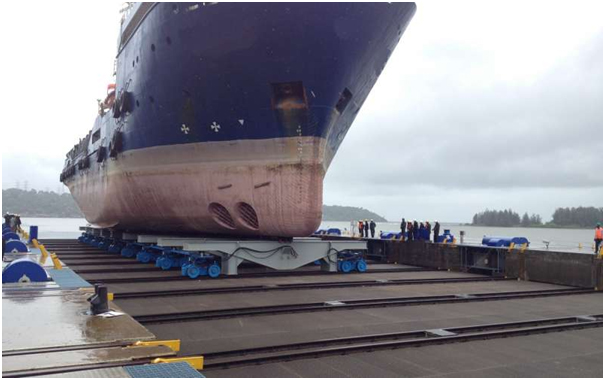
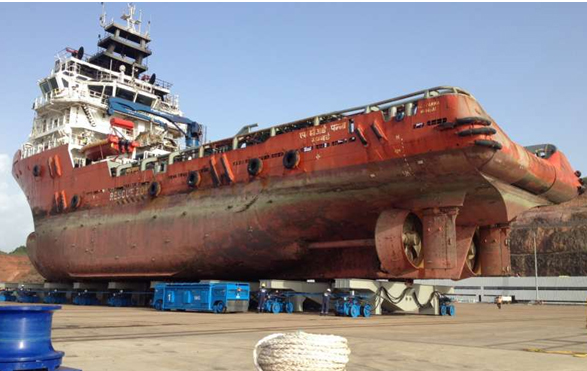
LAVGAN, INDIA
For more information please visit: www.img-tech.de